HUMBOLDT, Sask. — When Tyler Dies goes to work each day, he steps into a workshop where the air is thick with the heat of a blazing forge.
“When you realize what metal is capable of doing at your will if you add some heat and pressure… it’s amazing,” the blacksmith said, gazing proudly at a table full of his wares.
“I don’t like to make the same thing more than once,” he said in an interview with 650 CKOM. “Once I figure out how to make something, I kind of check it off my list as accomplished.”
READ MORE:
- How modern motherhood compares to my great-grandmother’s struggles
- Wash ‘n slosh: Warman laundry room houses hidden speakeasy
- Asquith school saves parents time, cash by buying bulk supplies
The list of items Dies has checked off is vast, ranging from corkscrews to railings and sculptures.
Each new creation he forges represents a meaningful step in his mission to preserve and celebrate his medieval trade in Saskatchewan.
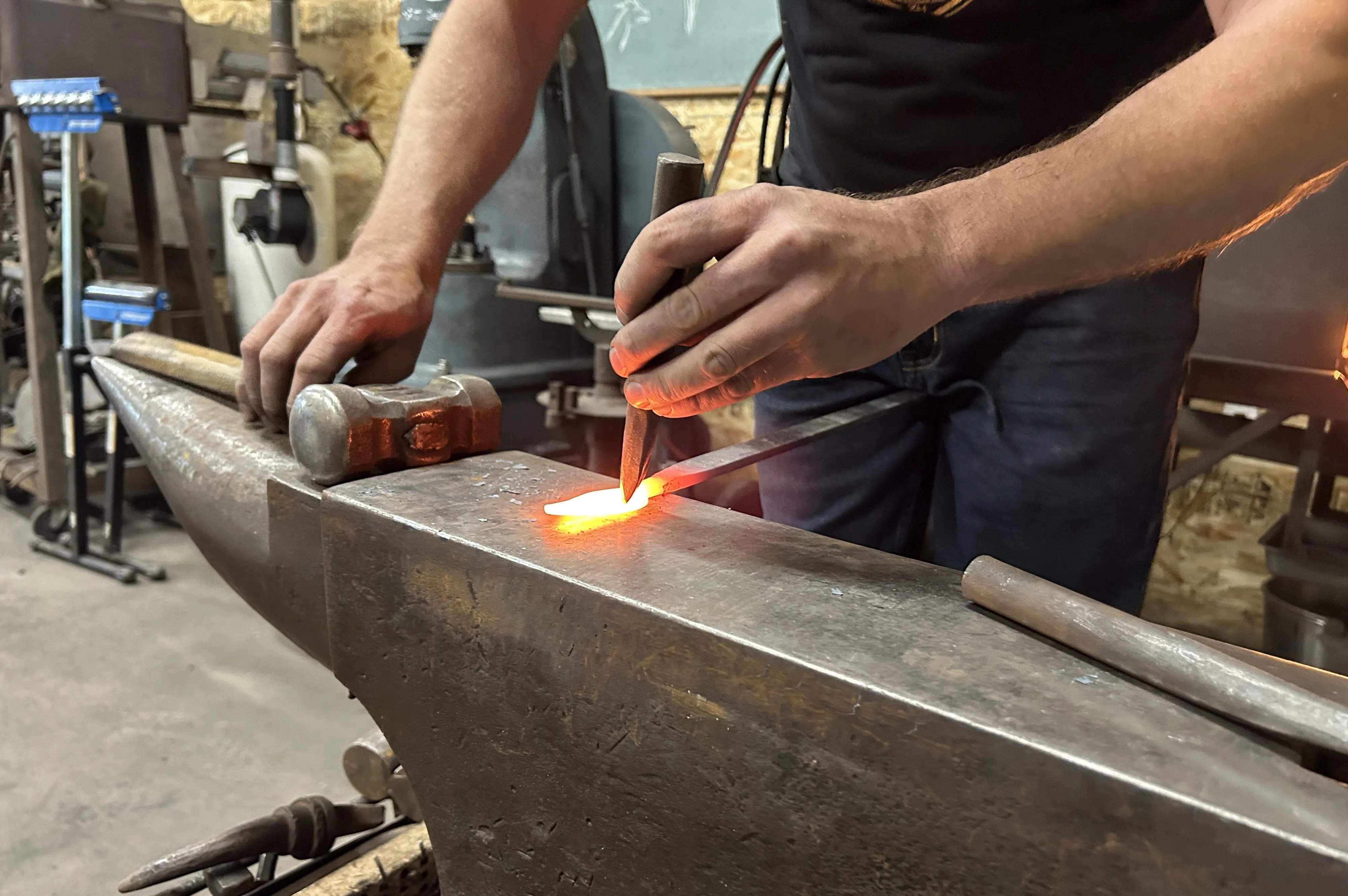
Early blacksmiths used simple tools like hammers and anvils — the same tools that are still used by modern blacksmiths. (Brittany Caffet/650 CKOM)
Blacksmithing started in ancient times, with the first evidence of iron working being traced all the way back to 1500 B.C. Early blacksmiths used simple tools like hammers and anvils. Those same tools are still used by modern blacksmiths.
Listen to Dies on Behind the Headlines:
“First, you need a heat source,” Dies explained. “Then, you need something to hit the metal with. A hammer. You also need something to hit the metal against, which is usually an anvil. A lot of people start with just a big block of steel, piece of railroad tie, something like that. And then you need material to work with. That’s pretty much it.”
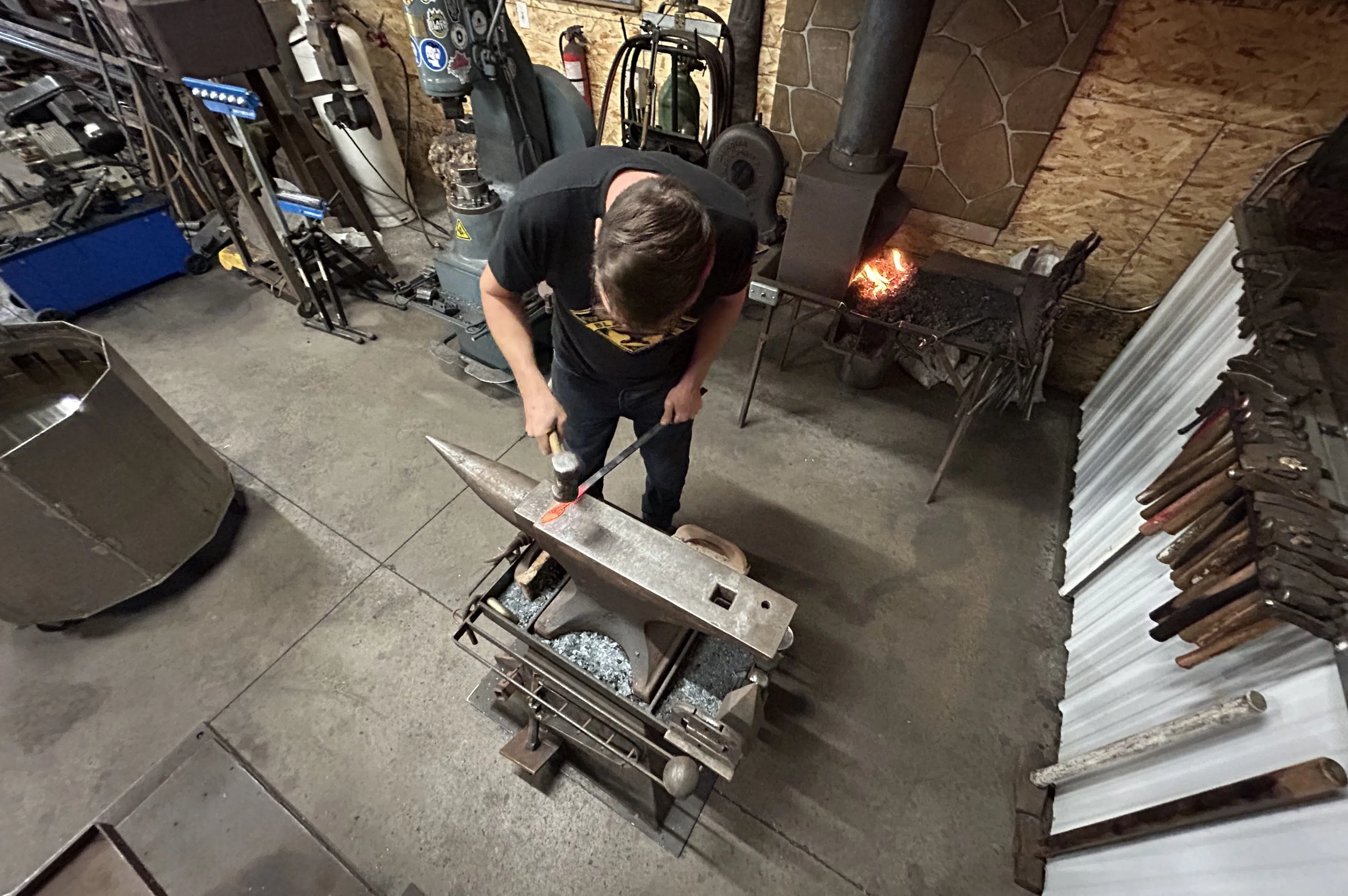
While many people assume welding and blacksmithing are similar, Dies said they’re actually quite different. (Brittany Caffet/650 CKOM)
Dies is no stranger to metal working. He is a welder by trade, but made the shift to blacksmithing full-time two years ago.
Welding and blacksmithing might seem similar at first glance, but they’re actually quite different. Welding focuses on melting metal pieces together with heat to join them, while blacksmithing involves shaping and crafting metal by hammering and working it by hand.
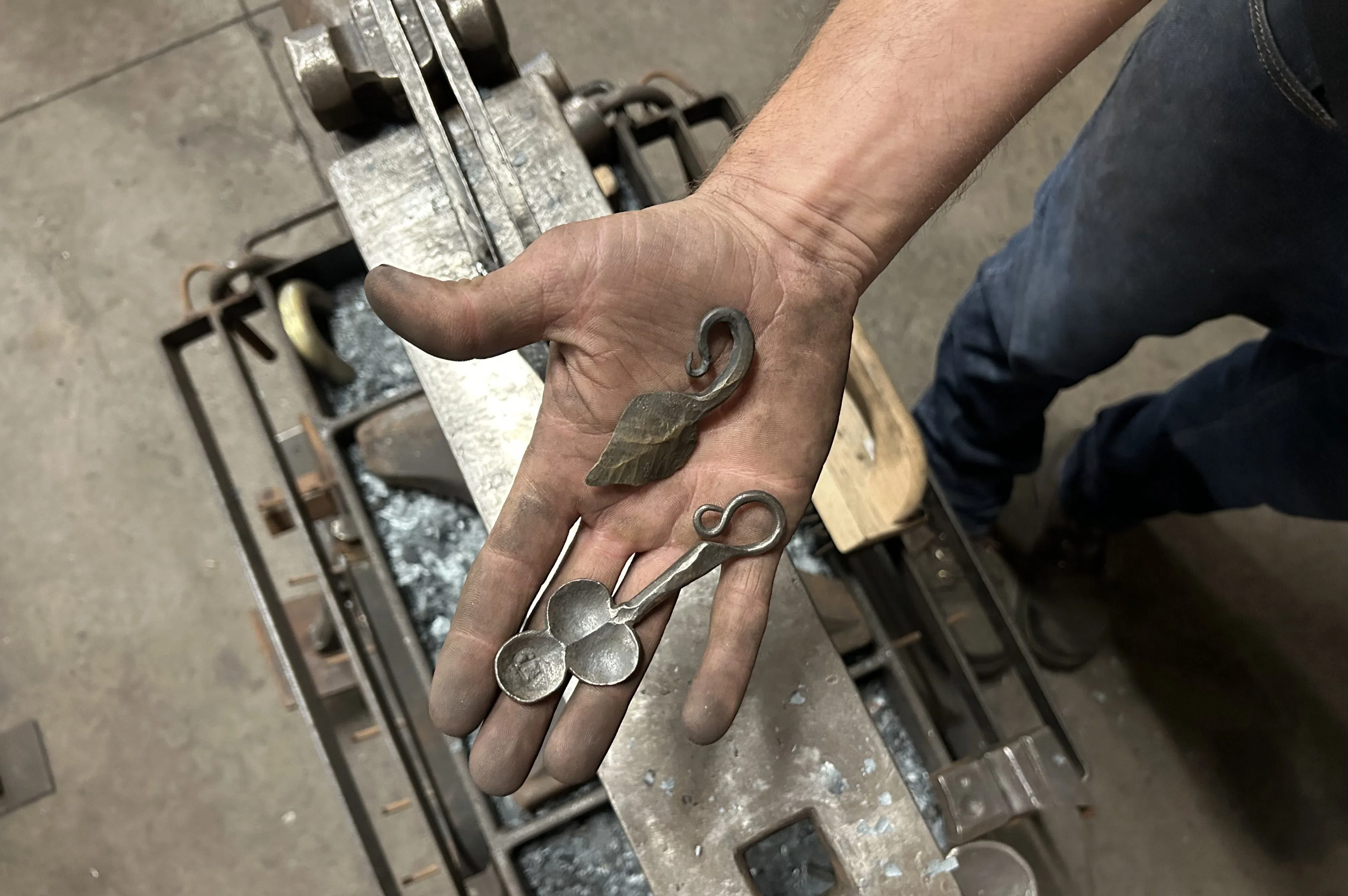
While metal workers stuck to creating things like horseshoes and tools in the past, Dies said thinking outside the box is crucial for modern blacksmiths. (Brittany Caffet/650 CKOM)
His first exposure to blacksmithing was 15 years ago through the Introduction to Blacksmithing course offered at the Western Development Museum in Saskatoon — a weekend-long crash course in the basic techniques blacksmiths use.
“I was hooked,” he said with a smile. “The combination of metalwork and blacksmithing was a pretty intriguing thing. Years go by, and I kept doing it as a hobby. When I was at work all the time, all I could think about was blacksmithing!”
He later switched gears and began accepting commissions for custom blacksmithing projects. While his most commonly requested items are fire pokers, he also gets a number of requests for larger, more challenging works.
“I was asked about a spiral staircase this week,” he said, adding that many people are shocked at the broad spectrum of items he is able to create from simple pieces of steel. “If it’s made of metal and I have the right tools to manipulate that metal… it could be anything.”
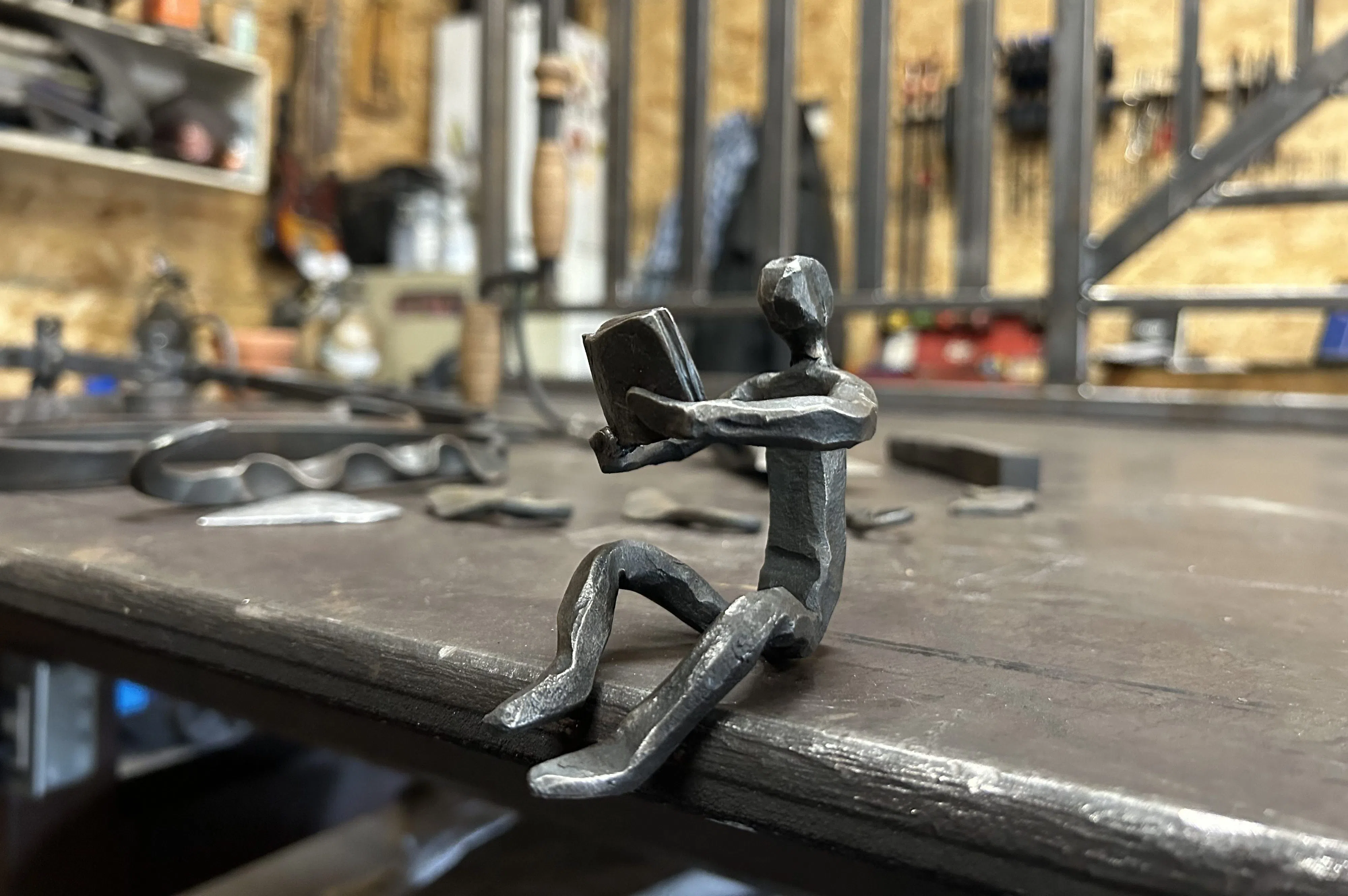
The list of items Dies has checked off of his to-do list is vast, ranging from corkscrews to railings and sculptures. This sculpture was made for a bookshelf in his daughter’s bedroom. (Brittany Caffet/650 CKOM)
While metal workers stuck to creating things like horseshoes and tools in the past, Dies said thinking outside the box is crucial for modern blacksmiths.
“If you don’t have the artistic or creative angle to your projects, blacksmithing doesn’t really have a place anymore,” he said.
“It’s quite time consuming, and that’s partly why the trade was dying, I think. People couldn’t afford to pay for the time it took to make things when you could do it faster with a welder or with modern tools. Today, it’s CNC machining, laser cutting, water jet and 3D printing metal… there’s a lot of other options.”
But even with plenty of innovative new tools available, Dies said he prefers to use traditional methods when it comes to metal work — and he’s far from alone in that preference. He said the number of blacksmiths in Saskatchewan is on the rise.
“There’s surprisingly more than you think. I can think of five that live in this Humboldt area alone. They’ve started to buy tools and get set up so that they can do it as a hobby, the same way I started,” he said, noting that the Internet has helped revive the age old craft.
“People now can connect better through social media, and also educate themselves through YouTube and other online forums.”
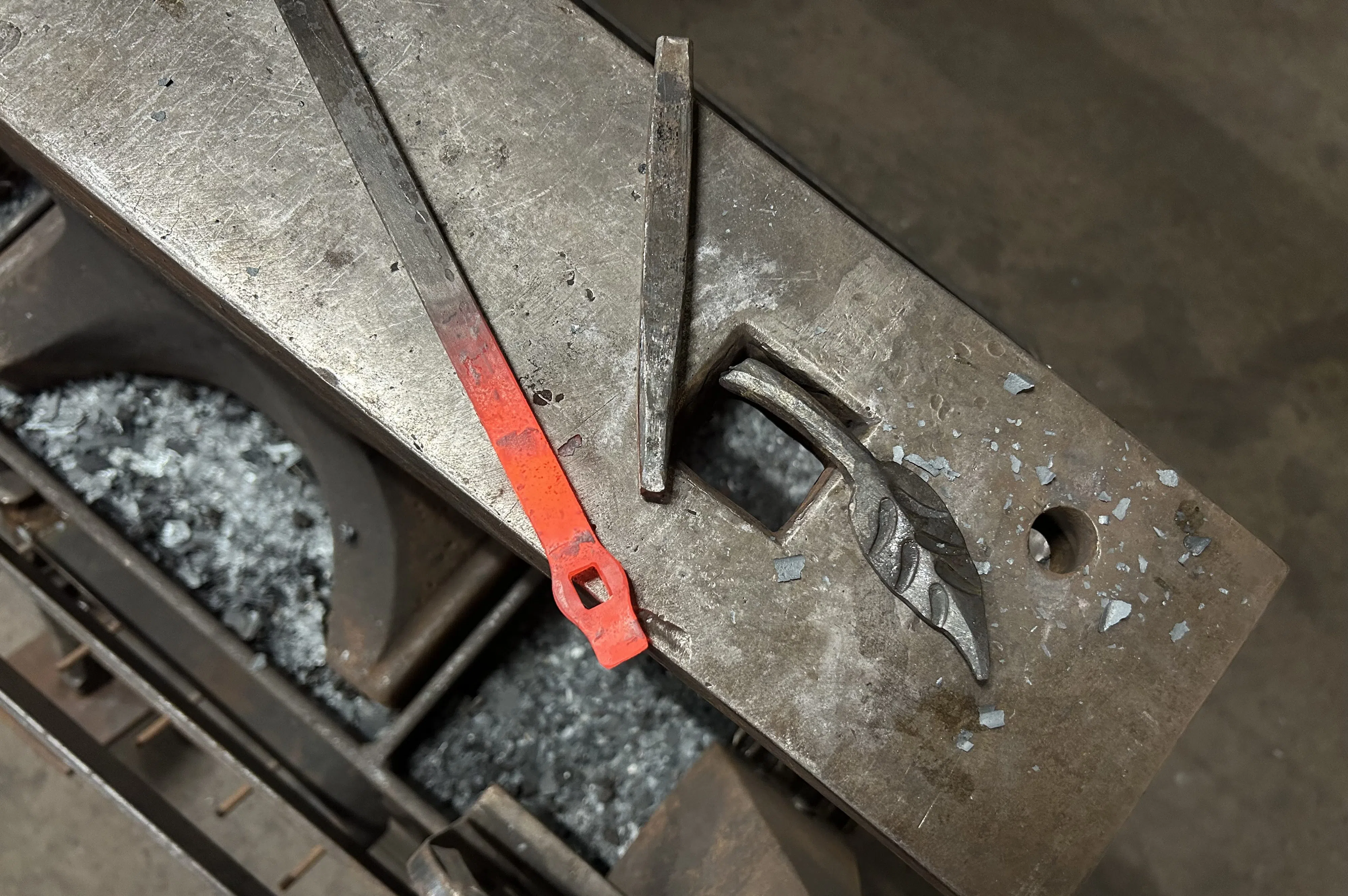
One of the blacksmithing techniques Dies has mastered is punching a square hole into metal. Its a technique utilized in many traditional blacksmithing projects. (Brittany Caffet/650 CKOM)
While a lot of learning takes place online, Dies said there has also been an increase of in-person gatherings in recent years.
“We have what are called hammer-ins. Just gatherings of blacksmiths that get together and help out people who want to learn a little bit,” he said. “Sometimes it’s about sharing tools. Some people don’t have the setup, so they show up at somebody’s shop and bring what they have and try to make something.”
And while these blacksmiths may build gates, they don’t gatekeep. Dies and his fellow experienced blacksmiths are passionate about sharing their knowledge with newcomers to the art form.
“We all want to share it and make sure it carries on,” he said.
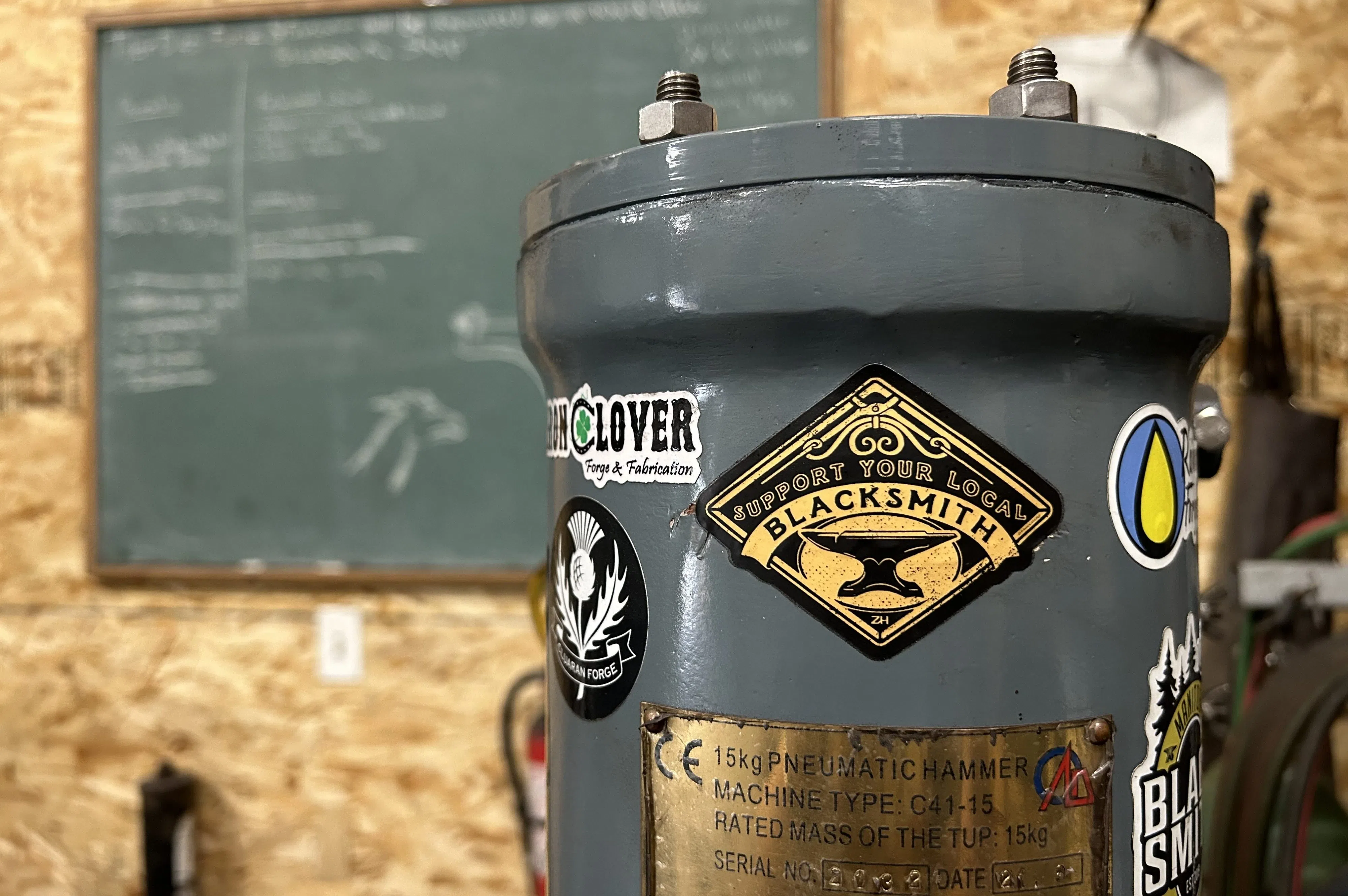
Tyler Dies said the number of blacksmiths in Saskatchewan is increasing with each passing year. (Brittany Caffet/650 CKOM)
While blacksmithing is typically a male-dominated trade, Dies said the number of women interested in the art form is increasing.
“I don’t think it’s 50-50 yet, but it’s not uncommon,” he said. “Some of the best blacksmiths I know are women. They just have what it takes to create cool things.”
Dies said he’s optimistic that as blacksmithing continues to expand across the province, more and more hobbyists will have the opportunity to make a career out of this medieval trade.
“There are blacksmiths still out there,” he said, a smile spreading across his face as he plunged his latest red-hot creation into a vat of cool water — his favourite part of the process.
“And we still want to make stuff!”