The Saskatchewan Research Council has become the first organization in North America to produce rare earth metals at a commercial scale.
According to the research council, the milestone was achieved this summer, and the council’s facility in Saskatoon is now ready to use its self-developed automated smelting technology to produce 10 tonnes of neodymium-praseodymium – which used to create powerful magnets – every month, with the purity level expected to exceed 99.5 per cent.
READ MORE:
- ‘Huge economic opportunity’: Sask. rare earth facility gets $16M boost
- New agreement means SRC expects to produce 400 tonnes of rare earths annually
- Saskatchewan’s rare earth facility takes another step forward
“SRC is on track to upscale this production to 40 tonnes of rare earth metals per month by the end of December, 2024,” the research council noted in a statement.
The facility is currently ahead of schedule, and is expected to be fully operational in 2025.
On Tuesday, members of the media were given a tour of the facility to learn more about how Saskatchewan is attempting to become a major player in the global market for rare earth minerals.
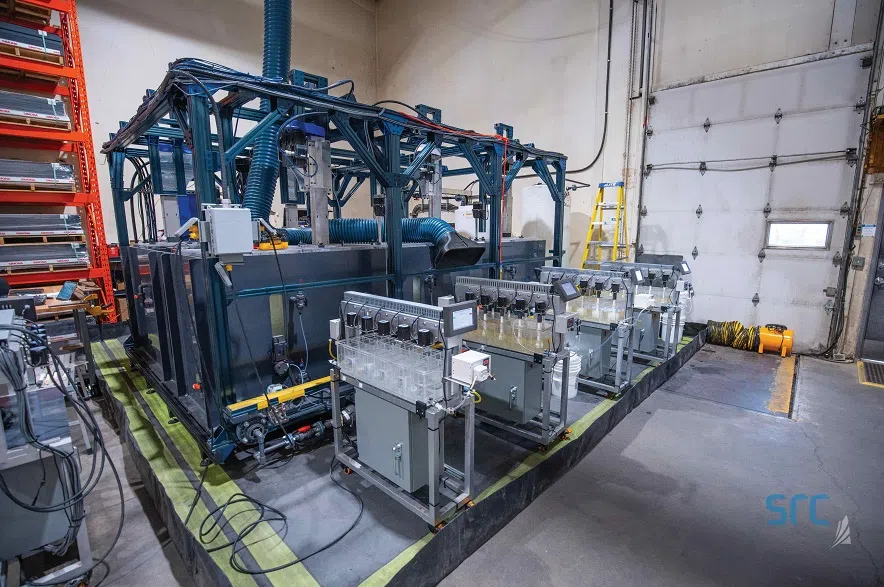
The research council’s proprietary solvent extraction cells. (Saskatchewan Research Council/Submitted)
Why does Saskatchewan want to produce rare earth minerals?
The main goal of the rare earth mineral facility is for Saskatchewan to begin producing neodymium-praseodymium metals with purities greater than 99.5 per cent and conversions greater than 98 per cent.
Once created and mixed, the metals are smelted into ingots, which can then be used in the construction of batteries for electric vehicles and other applications. When the facility is fully up and running, it is expected to produce enough neodymium-praseodymium metals to power 500,000 electric vehicles every year.
What is the economic benefit?
Once the production of neodymium-praseodymium metals gets started, Saskatchewan can sell the valuable materials on the international market.
“There is a very robust market for (neodymium-praseodymium),” said Mike Crabtree, the research council’s president and CEO.
“In the past two years, there has been a lot of interest outside of China to develop this sector,” added Dr. Muhammad Imran, vice-president of the research council’s rare earth elements division.
Crabtree said the Government of Saskatchewan, federal government and other North America allies are looking to build their own rare earth supply chain for North America, as the current supply is mostly controlled by China.
Canada is rich in monazite and bastnaesite, Crabtree said, which are critical to manufacturing rare earth minerals.
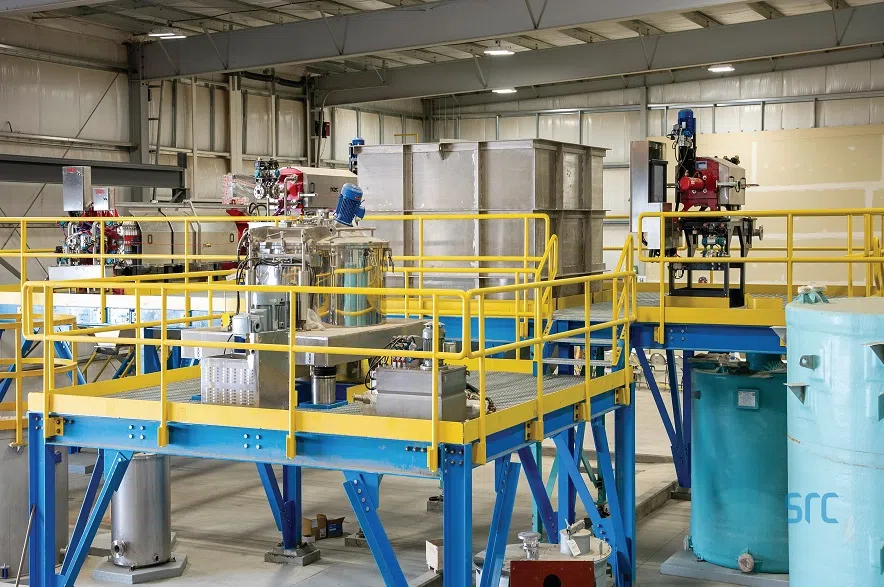
Equipment used in the Monazite Processing Unit of the SRC’s Rare Earth Processing Facility. (Saskatchewan Research Council/Submitted)
Each tonne of neodymium-praseodymium is currently worth approximately $2 million, and Saskatchewan is now producing the first commercial quantities of the material in all of North America.
By the end of this year, the rate of production is expected to reach 40 tonnes per month. The research council has set a goal of producing 400 tonnes per year, but Crabtree suggested that number could increase if all goes well with production.
“Four hundred tonnes per year in industrial terms sounds like a very small amount, but that sufficient for half a million electric vehicles, so it gives you some indication of the value of this metal,” Crabtree explained.
How are rare earth minerals made?
The first stage of creating the rare earth minerals is by taking monazite, a material which looks like black sand, and extracting all of the rare earth minerals from it. The output from that process containing all of the 17 rare earth minerals, which are then separated.
Five of the minerals, which are in the form of oxides, are then smelted into the metals, which can then be used for electric vehicles.
What does the future look like?
For now, the Saskatchewan Research Council is focused on getting the Saskatoon production facility completed and helping fuel the minerals to support the electric vehicle market in North America.
If things are successful, Crabtree said Saskatchewan could do more than just supply the minerals for electric vehicles. He thinks the research council could also become a supplier of chips that could be used in jet fighters.
“There are other metals that are required for defense purposes – for things like fighter jets and missile technology,” Crabtree said.
“A particular metal there is called samarium, and this facility here will produce sufficient samarium to provide nearly 25 per cent of North America’s defense requirement, which is really quite staggering from a commercial demonstration plant like this. Already, this plant this has significant defense importance.”
No decision has been made on whether the council will proceed with the extraction of samarium, but said a decision could be made in the coming months.
Made-in-Saskatchewan materials and use of AI
Crabtree said when the council was constructing the plant, one of the goals was to be a lot cleaner and safer than plants currently operating in China.
That meant Crabtree and his team had to get creative.
They created a new, made-in-Saskatchewan vessel for the smelting process, which involves extremely high temperatures. The work can be dangerous, and in places like China it takes a lot of people to run. In Saskatchewan, however, the process has been made mostly autonomous through AI, which will help make things safer.
AI has been incorporated into the 2nd and 3rd stages of the overall production, which are the solvent extraction and smelting stages, respectively.
In China and southeast Asia, the process usually takes dozens of labourers and can cause many problems, especially if there is an imbalance between water and the liquids being used. If there’s an imbalance, it usually takes months to fix it by humans, but because of the incorporation of AI, in Saskatchewan the issue can be corrected within a day.
“These plants are fairly large chemical plants, and they use vast quantities of water and chemicals. We made a very conscious decision that what’s going to be important for end users is to understand that these materials have been produced at the highest environmental standards, and are sustainable,” Crabtree said.
“The plant is going to be the most environmentally sustainable plant on the planet.”
— Editors note: This story has been edited for clarity.